We have come a long way from the stone plate. As you can well imagine, it would be very difficult to mount a piece of stone on modern high-speed presses. Senefelder’s first press was flat, so the use of stone was easy. Today’s presses use curved cylinders to hold the offset plates. The basis of modern lithography is a combination of photography and Senefelder’s original observation that “oil and water do not mix”. All offset plates made today employ this offset principle, they use as an image carrier such as thin paper, plastic, or a metal sheet which once exposed and processed can be wrapped around a cylinder of a press for printing. This modern offset plate contains two areas; image areas, which repel water (remain dry and accept ink) and non-image areas, which accept water. This is the basic requirement of all modern lithography – the ability to produce a plate which will have image areas that are “hydrophobic” (meaning water hating) and non-image areas that are “hydrophilic” (meaning water loving). While the basic principle is common, there are many differences between offset plates and the method they use to separate the image from the non-image areas.
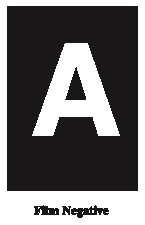
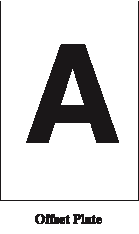
Today, the majority of lithographic plates are made of aluminum sheets of varying thickness (usually between .008″ and .0015″) with a surface grain or granular finish. This grain serves to give water-carrying properties to the plate and to give anchorage to the image forming material. Practically all plates are presensitized, that is they are supplied ready coated with a light sensitive diazo compound or photopolymer resin material ready for light exposure.
This photopolymer coating, as the term implies, is a chemical resin or polymer that will react with ultraviolet light – much like photographic film. When UV light strikes the photopolymer on the plate, it is “hardened”. Photopolymer that is not exposed to the light is not “hardened” and can be easily removed. This is the principle of the modern offset plate.
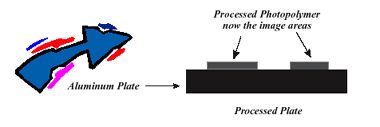
Exposing an Offset plate to produce a usable plate for the offset press
There are seven major types of lithographic plates used in the printing industry today:
- Diazo
- Photopolymer
- Silver Halide
- Electrophotographic
- Bimetal
- Waterless
- Spark Discharge (digital waterless)
- Laser (digital waterless)
- Computer-to-plate – Various types of Plate Material
Film positives and negatives along with digital information (computer) are used for making or exposing most types of offset plates today. While there are several types of offset plates, they are all generally classified as either positive or negative working plates.
Negative-working plates are comparatively inexpensive and commonly used in the United States. As the name implies, film negatives are used to image the negative working plate. These plates are generally coated with a photopolymer and are known as negative working presensitised plates. Exposure and processing of this type of plate is usually within ten minutes. To expose the plate, a film negative is placed over the light sensitive coating and exposed to UV light. Light that passes through the clear areas of the negative causes a reaction with the “monomers” of the photopolymer which chemically cross-link with each other to form polymers. These polymers can be thought of as complex chains of monomers, which are linked so strongly, that they behave as a single, hard, wear-resistant molecule. The actinic light cannot pass through the black areas of the negative so no reaction takes place with the polymer under the non-clear areas of the negative. Processing removes unexposed non-hardened polymer. An application of a gum solution to the non-image areas of the plate to make it water-attracting/ink rejecting. The processing does not wash off the hardened polymer image areas of the plate.
Positive working plates are more expensive than their negative-working counterparts. These types of plates are used more by European printers. As the name implies, film positives are used to image this type of plate. The photopolymer used to produce a positive working plate is different from the polymer used in the negative working plate as it is hardened before exposure. The photopolymer used here becomes unstable when exposed to ultraviolet light and remains hard where no light strikes the polymer. Plate processing is similar to the negative plate except that the processor removes the exposed photopolymer from the plate and applies a thin layer of gum to protect the non-image areas from ink.
Plates are generally made from aluminum. Other base materials can be used such as paper, polyester and multi-metal. Multi-metal plates are used for long extensive press runs due to their durability. Paper type plates are used in small offset presses known as duplicators for very short runs (1,000 – 10,000 impressions). Polyester plates may be used in small press or in larger sheetfed presses. Like paper plates, these are intended for short runs. In general, the polyester and paper plates are much less expensive than the aluminum or multi-metal plates. Cost, run length, type of press and the type of job dictate the type of plate used by a printer.
Offset Plate Technology
The aluminum-based plate contains the light-sensitive coating applied or coated over the aluminum. Paper and polyester plates are treated very similarly. The multi-metal plate, however, is similar but the structure of the base plate is slightly different from that of the aluminum, paper, etc. Multi-Metal Plates were developed to extend press run life. In general, multi-metal plates are presensitized polymer plates consisting of a metal base with one or more metals plated to it. Today, there are two basic types of “bi” or multi-metal plates:
- Copper plated onto stainless steel or aluminum
- Chromium plated on copper
They are the most durable and the most expensive. These plates can be coated with either diazo or photopolymer and can be either negative or positive working.
They are designed with a purpose in mind. In most cases, a major determining factor is press run length. A long run length, for example, on a small offset duplicator might be 10,000 impressions (copies) with a short run length being in the neighborhood of 2,000 impressions. When you talk about larger commercial 4 to 6 color sheetfed presses, short run lengths would be around 20,000 with long run lenghts being up to 100,000. High speed webs differ even more. Long run lengths generally will be in the 1,000,000 impression range. So it is difficult to give a generalization of run length for a particular plate.
Diazo – is a compound used to coat the offset plate. Diazo coatings are organic compounds that are used to make presensitized plates with a shelf life of about a year and for wipe-on type plates that can be in-plant coated with a shelf-life about one to two weeks. These plates can be both negative or positive working. Once exposed, they are treated with an emulsion developer which consists of a lacquer and gum in an acid solution. As the unexposed diazo is dissolved by the solution, the gum deposits on the non-printing areas ensuring water receptivity. The lacquer deposits on the exposed areas making them ink receptive. Once developed, the plate is rinsed with water and coated with a protective gum arabic solution. Run lengths are short with these type of plates. Run lengths of 100,000 to 250,000 impressions with web and sheetfed presses can be achieved.
Photopolymer – coatings used to make photopolymer plates are organic compounds which are very inert and abrasion resistant, allowing longer press runs than diazo coatings (up to 1,000,000 sheetfed or web impressions). This type of coating is the most widely used material in platemaking. Plates made with photopolymer can be both negative or positive-working. The photopolymer coating is different from other sensitizers as they change in molecular weight during exposure. This accounts for many of their unusual properties such as long runs, resistance to abrasive wear and increase in wear resistance after baking (processing technique to extend run length). Today, new high-speed photopolymer plates have been developed with a dye sensitized photopolymer that can be exposed by laser and used in digital imaging systems (computer based desktop systems). The photopolymer plates are by far the most widely used plates in the printing industry today.
Silver Halide – are high speed plates that use a photosensitive coating similar to photographic film except that the silver halide emulsions are slower. The emulsions are color-blind and very light sensitive in the blue region of the visible spectrum so they have to be handled in yellow filtered light. This type of coating can be exposed optically using negatives or by lasers from digital data. The processing solutions contain heavy metal (silver) by-products which must be either carried away to special treating plants or treated in-plant with silver recovery chemicals before being allowed to drain into municipal sewers. Film-based plates are used to print single color business forms, reports, etc. from digital information. These plates may also be exposed like photographic film in a large camera then following exposure, developed and placed on the press for printing. Silver-halide plates are used for spot and process color reproduction using digital data. These types of plates are popular with short run, quick turnaround printers.
Electrophotographic – plates are based on the principles of the electrostatic copier. There are two types of plates:
- Inorganic photoconductor on a drum
- Organic photoconductor on a substrate
The photoconductor is sensitized to light by charging with a corona discharge. The charge is dissipated in the areas exposed to light. The charge remaining on the unexposed areas attracts a dry or liquid toner with an opposite charge. The base photoconductor material used is normally selenium or cadium sulfide coated onto paper, plastic, etc.
Plates for laser imaging are coated on electrograined anodized aluminum. During processing, the coating must be removed in the non-printing areas, and the plates are treated with etch and gum to make them water receptive. In the chemical removal process the image elements (dots) become slightly ragged which can affect their use for fine screen, high quality process color printing. Another type of electrophotographic plate is the Zinc Oxide paper plate used by quick printers. These plates are very similar except the Zinc Oxide is the photoconductor. These types of plates are normally used for short run duplicators by quick printers.
Waterless plates – are similar to the conventional offset plate except that a layer of silicone is applied on the surface of the light sensitive photopolymer. The thin layer of silicone is bonded to the photopolymer. Exposure is similar to that of the conventional offset plate. Exposure light passes through the clear areas of the film negative and silicone layer striking the photopolymer material beneath. The light activates the photopolymer, causing a break in the bond between the photopolymer and the silicone layers. Areas where light does not pass through negative, no break in the silicone bond occurs. Processing removes the un-bonded silicone leaving only the photopolymer which is ink receptive. Silicone rubber has a very low surface energy and is not wet by the ink.
Systems have been developed for waterless printing using special ink temperature control systems on press to assist in stabilizing the ink and its viscosity. Waterless plates can be either negative or positive-working. This type of printing has advantages as it eliminates the gum-water based fountain solution. Fountain solution, as it emulsifies with the ink, can dull printed colors, increase dot gain and make controlling the press more diffi cult. Printing with the waterless process allows the printer to print with finer line screens (300 lines per inch and higher) due to the absence of the fountain solution resulting in higher resolution pictures. The plates, due to the silicone, have shorter run lengths (under 100,000) and scratch easily requiring press shutdown for plate repair. This type of system is also more expensive than the conventional offset plate.
Heidelberg GTO-DI (Direct Imaging) – plates are used on the Heidelberg GTO-DI press system. These plates are very similar to the above waterless plates except they are imaged on press by computer. In a way, the press is the printer for the computer much like a dot matrix printer is. The plates are imaged in this case, however, by lasers. The plates are made in a three layer composition. The base material is either polyester or aluminum. The middle layer is an infrared-absorbent material. This layer matches the laser’s output wavelength and its role is simply to vaporize when struck by the laser light. Over this layer is a thin layer of silicone. As the laser strikes the plate, the infrared vaporizes and loosens the silicone layer which is wiped away following imaging. The wiped area is now the image area as no silicone remains. The non-image area is the area containing silicone which was not removed during the imaging process.
The same plate and technology is used in the Heidleberg Quickmaster DI-46-4 press with the exception that instead of a single plate a plate roll is used. See the first section under Printing Processes for a more detailed description. These plates are very short run plates (under 25,000 impressions). Once the plate has been imaged, the waterless process is near similar to the above waterless plate. These plates are near similar to the Toray Waterless plates mentioned in the Waterless Section in the previous page.
Heidelberg Quickmaster D146-4 (Direct Imaging) – Like it’s predecessor the GTO-DI, the Quickmaster uses a waterless plate. Unlike the earlier versions of the OTO-DI (which used the “spark” imaging system) the Quickmaster waterless plate is imaged via an laser array. Data (Postscript level 2) is converted in the RIP (Raster Image Processor) into screen data, which is in turn converted into control signals for 64 infrared laser diodes (16 diodes per printing unit) in the printing press. An Ethernet interface is sufficient to transmit digital documents from the prepress directly without film exposure, plate exposure and stripping tot he Quickmaster DI. The laser beams created by the laser diodes are led to optics via fiber-optic cables, and are bundled into a precise ray of light. On a special, multi-layer plate very small sharp-edged depressions are created through high levels of energy. Analogous to other dry offset processes these depressions accept ink, which is repelled by a silicon layer on all other places on the plate. The system can image up to 1,270 dpi or 2,540 dpi. This is sufficient for printing a 150 Ipi screen in very good offset quality. Imaging time ranges from 6 minutes (1,270 dpi) to 12 minutes (2,640 dpi). Since all four printing units are imaged at the same time, all are in registration. The plate itself is very similar to the waterless plate used in the GTO-DI with the exception the plate comes in roll form (see Printing Methods, Section 2). Like with the OTO-DI Waterless plate, the Quickmaster plate is on a mylar or polyester base and is flexible.
MAN Dicoweb or the CTPress (Direct Imaging) – Meaning “Digital Change Over Web” is the latest digital technology to hit the printing scene, however, it is not yet commercially available. The Dicoweb works by printing digitally to a “plate” cylinder, printing the job and then cleaning the “plate” cylinder for re-imaging. The process works by using a laser head to directly image the printing cylinder via a thermal ribbon. The thermal material transferred from the ribbon to the plate cylinder (which is actually a sleeve). The thermal image laser deposited is ink receptive. The areas of the cylinder that received no thermal material are the non-image areas which accept no ink but fountain solution instead. After the completion of a print run, the cylinder surface is automatically cleaned by a device similar to a blanket washer. Once washed, the cylinder is reading for more imaging. See the Printing Methods Section for more details.Continued on the Next Page Offset Plate Technology
Computer to Plate (CTP) – Computer to plate systems today can use a variety of plate material – depending upon the manufacturer, system design, etc. CTP systems can use several systems which include:
- Silver Halide
- Thermal
- Direct Thermal – Requires the use of a special substrate that changes color when exposed to heat.
- Thermal Transfer – This approach uses a thermal array to transfer colorant from a ribbon to a substrate.
- Photopolymer
- Ink Jet
- Hybrid
No matter how what technique is used, the end result is the same; an offset lithographic plate with the image areas that will accept ink and a non-image area which will accept no ink. Computer to Plate is a technology whose time has come. It was only a few short years ago when only 2 or 3 major vedors were available, now today there are over 46!