With all the high speeds and productivity needed in today’s sheetfed market, How does the printer keep it all together?
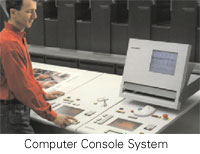
20 or 30 years ago most of the process was hand driven in other words all press operations were completed by hand. If you needed to adjust ink, you did it by “tweaking” the “ink keys” at the ink fountain which meant climbing up to the ink system on the press. Most of the rollers also needed to be engaged by hand. Ink levels and print quality was left to the eye of the press operator which of course varied over the course of the day. When a new job came to press, the press operators had to “eyeball” the plate and make a guesstimate as to where the ink keys and fountain should be set – a trial and error method. Today, however, is much different as automation and computerization has set in. Today’s modern sheeted-presses are fully automated with internal computers do assist the press operator. Presses can come equipped with a “plate scanner” and computer consoles to do many of the tasks the press operator did by hand years ago.
oday when the offset plate comes to the press, the press operator can scan the plate on a “plate scanner” (if equipped). The image densities are read across the individual plate and the fed into the press console which can then preset the ink keys and the ink fountain (total ink flow). The operator can scan the black offset plate, for example, via the press computer the black ink unit would be preadjusted based on the readings taken from the plate scanner. The same would be done for all the additional plate colors such as cyan, magenta, yellow and any other special colors.
Plates today can be automatically “hung” or mounted as well as be removed without operator interaction. Cleaning of the blankets today also is fully automatic. Once the plates are mounted make-ready begins. While the plate scanner will be close in color and density, the operator usually has to make some small adjustments on color and registration. Unlike in years past, however, the operator can do this electronically through the press console. With a image scanner attached to the press (closed loop) the press sheet can be scanned using color bars. This device measures ink density and relates it to ink film thickness. The operator can read the results via a computer screen. By electronically activating the ink keys and fountain via the press console adjustments are made quickly and easily compared to years past.
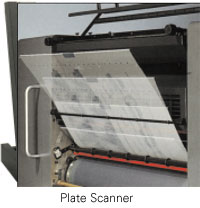
Once the customer or press operator has approved the color the press operator can “lock” the values into the computer. During the press run the operator will scan sheets every so often on the scanner to measure color. If a color starts to shift out of tolerence, the scanner will display that information and the operator can “send” the data over to the press computer which will automaticity adjust the proper ink unit to bring the density levels back in customer tolerance. Some modern presses today even have the color system “closed looped” fully so small adjustments are being made continuously. You can do the same with an off-line scanner or hand held scanner, however, the press operator will make a judgement call based on their experience on changing the ink level (via the press console). What has this done? Well, it has speeded up make-ready time by as much as 85% which in turn reduced cost and increases productivity.
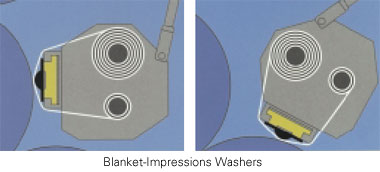
With any manufacturing process, and printing is a manufacturing process, productivity is a must!
This unit is programmable from the press console. A cloth material is installed in the unit. As it washes, with press solvent also being applied, the cloth material will “wipe” the debris and solvent away. At the conclusion of each wash the cloth will advance. After a while the cloth unit needs to be replaced with a new cloth unit.
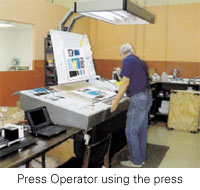
Important Properties
- Paper Consistency
- flat and dimensionally stable
- Good surface strength
- Surface cleanliness
- Good slitting/cutting – clean edges
- Accurate and square cut