Flying Splicer

“Flying Splice” – As the main feeding roll nears its end, the roll stand is rotated to bring the next full roll of paper into running position. This is done with the press running at full or operating speed. Double-sided tape is applied to the leading edge of the new roll. The new roll is moved into contact with the running roll of paper. The taped edge of the full roll is pressed against and immediately adheres to the running roll. Paper from the depleted roll is cut off and the roll brought to a stop. The old core is taken off and a new roll is then place on the backstand. As mentioned earlier, this type of splicing system is usually used on wide offset and gravure presses greater than “38.”
Zero Speed Splicer
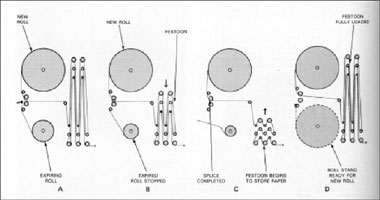
“Zero Speed Paster (Splicer)” – This splicer differs from the splicer above in that the old and new roll stop momentarily during the splicing process while the web press continues to run. To start the splicing process a new roll is positioned and taped. When the feeding roll nears its end, the paster unit festoon draws out considerable slack in the running web which allows both the new and old roll to stop momentarily. To make the splice both the old web and new web make contact momentarily and the tape is contacted from the new roll to the old running roll. The web is cut from the old roll an the new roll allowed to come up to web speed. These operations are performed before the slack in the festoon is absorbed or taken up.