Offset press blankets are made of supporting fabric and a rubber composite. Various rubber materials are used for the transfer of the image from the plate to the blanket. Blankets come in compressible to hard finishes along with smooth to rough surfaces. The majority of printers today use compressible type blankets. These blankets give good compression which eliminate many smashed blankets. Slightly rough blankets are also preferred as they have less contact with the paper surface thus reducing blanket contamination.
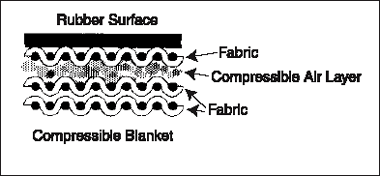
Offset compressible blankets are constructed from two, three or four plies of a strong woven fabric fastened together with thin layers of “rubber” adhesive to form a laminate termed the carcass. The carcass then receives many coats of a suitably compounded polymer, applied to one side to produce the face layer which is approximately 0.020″ thick Total thickness, i.e. face and carcass together, is between 0.030″ and 0.075″, depending upon the number of fabric piles employed. The number of fabric layers equals the number of plys. Thus a 4 ply blanket would contain 4 fabric layers. To make the blanket “compressible” a thin layer of air cells (for compression) is layered between the fabric and rubber face. Conventional blankets are made up of a rubber face and the fabric carcass. A compressible blanket is made up of a rubber face, fabric, compressible layer and a carcass.
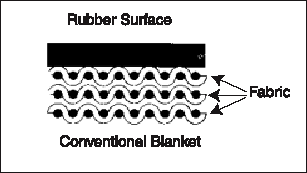
The conventional blanket will bulge at the printing nip (displace not compress), especially when over packed. The conventional blanket is good when blanket packing is critical, however, squeeze pressure must be precise. The conventional blanket is recommended where high print pressures are required. The compressible blanket, on the other hand, will form only a very slight bulge when overpacked.
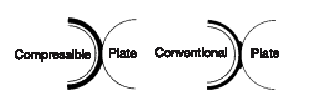
The diagram above shows the difference in compression between the compressible and the conventional blanket
Unlike the conventional blanket the compressible blanket has many more features such as:
- Smash resistance which translates into longer blanket life
- Compensates for variation in Blanket thickness and substrate
- Wider latitude for packing
- Reduction in plate wear
- Reduction of slurring
- Minimizes mechanical press problems
Blankets are manufactured in three types of surfaces:
- Cast – Surface finish produced by curing paper and talc
- Ground (buffed) – Mechanical process of finishing the surface of a blanket
- Texturized – Surface finish produced by chemical means
Below are magnifications (100X) of various blanket surfaces (Cast, Buffed and Textured)
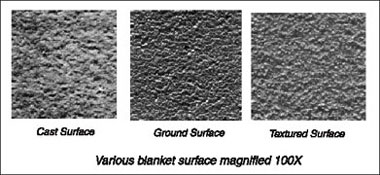
Blankets will generally last 3 to 6 months depending on the type of press (web/sheetfed) and types of jobs run. Conventional blankets are hard and give a high amount of resistance when the blanket and plate cylinder are squeezed together, as shown in the drawing on the next page. Compressible blankets, as their name implies, are compressible and give under the squeeze.
Properties required in an offset blanket:
The fabric piles must be strong and stretch very little. There should be, however, some degree of stretch to allow the blanket to fit tightly on to the cylinder, since a slack blanket can cause doubling and slurring. On the other hand, excessive tensioning through high stretch will cause uneven thickness and result in low areas in the print. The thickness must be uniform between closely defined limits.
With an compressible blanket, slight bulges do form, but to a much lesser degree than the conventional blanket. Compressible blankets are used to print uncoated and lighter coated papers. When a blankets wrap occurs, due to a web break or paper sticking to the blanket, the compressible blanket has the best chance for surface recovery. The conventional blanket, due to its very hard surface, will not retract like the compressible surface.
The conventional blanket bulges at impact point. Rubber displaces rather than compresses and will bulge when subjected to pressure. Because of this displacement, the surface speed of the conventional balnket is slightly different than the surface speed of the plate. One possible result is slurring. Conventional blankents can be used when highly coated papers.
The face of the blanket should be
- free from pinholes, and blemishes which could affect print quality non-abrasive to reduce plate wear
- resilient
- of uniform surface hardness and hard enough to be capable of reproducing a facimile of the printing image
- very smooth, having a matt surface with no low spots or raised areas
- resistant to ink vehicle, cleaning solvent and varnish
- ink-receptive
- resistant to peeling, blistering, embossing, debossing, glazing or tackiness, also abrasion from paper or board
- capable of giving good release (ink and paper)
Packing is very important to the life of a press, blanket, plate, etc. When a new blanket is put on a press, it will first stretch. Usually the pressmen will, after installing, run the press under impression for several hundred or thousand impressions then retorque the blanket. Blankets should always be torqued to assure proper tension. To attain the proper squeeze between the plate and blanket (to assure proper transfer of the image) special paper, known as packing material, is placed under the blanket and plate. A special “packing micometer” is used to determine the amount of packing material needed. See page 3-35 for a diagram of blanket packing. It is important that you always recheck packing, after installing a new blanket, several thousand impressions after.
- Common blanket problems include:
- Incorrectly installed (over/under packed)
- Overtightened – hand vs. torquing
- Poor blanket maintenance – using harsh cleaning materials that contain acetone, toluene, etc.
- Out of square blanket
- Wrong blanket for application
- Poor release blanket
As there are many types and styles of blankets, the printer must evaluate the type of blanket he wishes to use and work with a blanket supplier such as Day International. Most printers are printing a wide range of papers and can not change a blanket for every paper printed. A printer must work with a supplier and choose the right blanket that gives him the best overall performance for a wide range of papers printed.
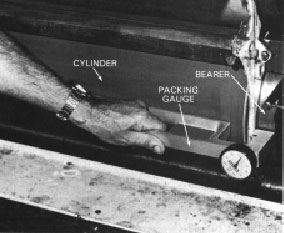
Using a packing gauge
How to pack a blanket…
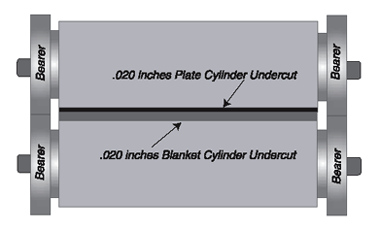
Plate cylinder is .020” undercut. The offset plate is .012”thick. To bring the plate to a pressure squeeze of .004” (over bearers) we need to add 0.012” packing material.
The blanket cylinder is .090” undercut and the blanket is 0.065” thick, then 0.025” packing is required to bring the blanket to the surface.
This then will allow the squeeze to be 0.004” between the plate and the blanket.