The conventional or Direct dampening system employs a fountain roller which picks up the fountain solution in the fountain pan. A ductor roller takes the fountain solution from the fountain roller and passes it to a distributor roller. From here the fountain solution is transferred to the offset plate via one or two fountain form rollers. The ductor and form rollers (rollers that contact the plate) of the system usually have a cloth or paper cover which some printers call a “sock”. In years past they were known as “molleton” covers. Today the rollers are covered with 3M paper sleeves or a fabric type such as Veratec Red Runners.
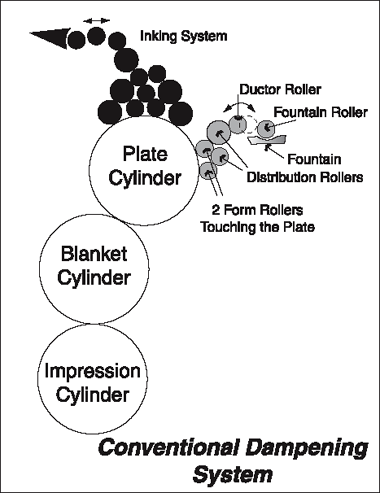
A drawback of this system is the slow reaction time in making adjustments due to the “back and forth” action of the ductor. Also the cloth covers become soiled with ink and need cleaning, otherwise they can transfer the ink to the non-image areas of the plate.
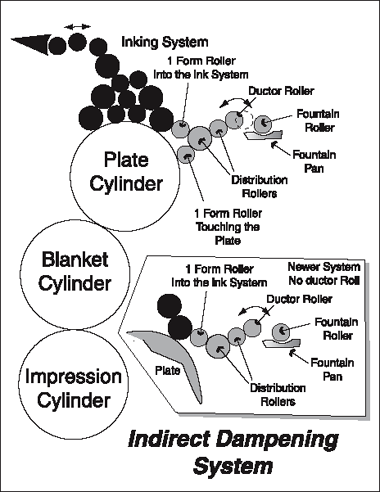
The Indirect conventional dampening system feeds the fountain solution directly into one of the ink form (roller that touches the plate) rollers. This system is known as “indirect” since the fountain travels to the plate via an ink form roller and not directly to the plate as the above system does. Some indirect systems, such as the one shown on the right, will have the ability to feed the fountain solution into the ink system as well as to the offset plate. A ductor roller still picks up the fountain solution and transfers it to the transfer rolls and then to the form rollers. Most newer presses today, however, do not employ the ductor roller but use a continuous feed system (see inset).
A fine emulsion of ink and water is then developed on this ink roller. This is one reason printers need to know about “water Pickup” or what percentage of water can be taken up by the ink. This system is also known as an “integrated” dampening system as it is integrated into the ink system. One of the benefits of this system, is that is does not use covers thus it reacts quicker when dampening changes are made.
You generally find this type of dampening on newer and faster press equipment today.
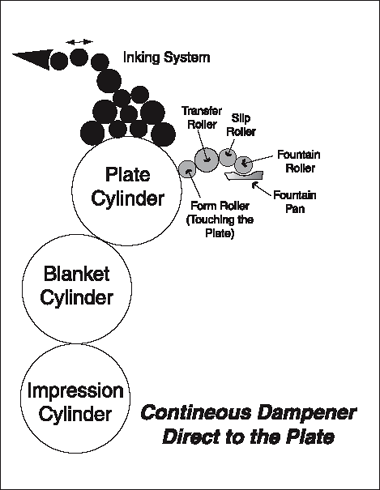
The continuous dampener is actually a roll type coater. There area two types of continuous dampeners – one type feeds fountain solution directly to the plate and the other feeds it directly into the ink system. The continuous dampener uses a four roller system:
- Fountain Pickup roller
- Slip roller
- Transfer roller
- Water form roller
The slip roller controls the amount of fountain solution supplied to the plate. Speed the roller up and you feed more fountain solution. Slow it down and you supply less. The use of alcohol on these type of dampeners was standard for years. Alcohol (Isopropyl Alcohol) was used as it increased the fountain solution viscosity and made it “more wettable” so that transfer was easier from one roller to the other. The Government, however, has pushed to eliminate the use of alcohol as it is contains VOC’s (Volatile Organic Compounds). Alcohol substitutes such as Glycol ethers, Butyl Cellusolve, etc., are being used today to accomplish the same task. Roller hardness is also being changed to help accomplish the same job – easy transfer of the fountain solution.
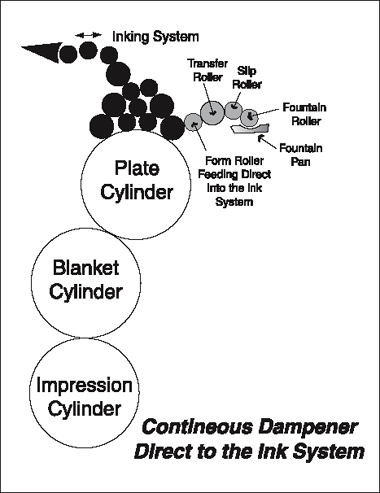
Continuous dampeners can either feed directly to the plate (above) or directly into the ink system (right). Advantage can vary but usually is determined by the press manufacturer.
Recall that most lithographic plates function on the principle of water and ink receptive areas. In order for ink to adhere only to the image areas on the plate, a layer of moisture must be placed over the nonimage areas. The dampening system accomplishes this by moistening the plate consistently throughout the press run.