Fountain solutions as used on a offset press to keep the ink from adhering to the non-image areas of the offset plate. There are seven key functions of a fountain solution:
- Keep ink off the background with a film of water
- Maintain the hydrophilic nature of the background
- Quickly clean ink off the background during press starts
- Promote fast spreading of water over the plate surface
- Help the water flow evenly through the dampening rollers
- Lubricate the plate and blanket
- Control emulsification of ink and water
Fountain solutions generally consist of five major parts:
- Water – which comprises by far the largest portion of the fountain solution.
- Acid – which reducing the pH, keeping the plate image area sensitive to ink as well as keeping the background areas sensitive to water
- Wetting agents – or surfactants lower the surface tension of the water allowing it to maintain the wetting characteristics of the non-printing areas (non-image areas) of the plate. By reducing the amount of water necessary to keep the plate clean, they also reduce the amount of ink required for printing. Isopropyl Alcohol was one of the most favorite wetting agents added!!
- Plate conditioners/additives – minimize the corrosive action of the acid on the aluminum plate. This willextend plate life and improve the overall print quality. Most solutions also contain antiform and anti-fungus agents. Fountain solutions may also contain buffering compounds to keep the solution acidic, non-piling agents (NPA) to eliminate any chance of piling, silicone materials to enhance the release characteristics of the blankets and minimize piling due to paper picking tendencies, etc.
- Gum arabic – added to the fountain concentrate today. The gum뭩 function is to adhere to the plates?non-image area and protect it from accepting ink. Gum also serves to protect the plate from humidity and chemical attack during press stops. Today, some gum substitutes are being used such as CMC (carboxymethyl cellulose), etc. Gum arabic, however, is still the most effective material for keeping the non-image areas of the plate clean.
In general, the gum, conditioners, additives, acids are combined into what is known as “fountain concentrate” or “fountain etch”. This solution is purchased by the gallon or drum and added to water.
In the past, these three ingredients would be mixed at press side by someone in the printing department. They would be controlled according to the manufacturer뭩 specification. Since, however, they are proprietary compounds, it is important that the printing ink formulator be aware of the specific types of fountain solutions that will be used by a customer (printer).
Today there is a trend to move away from the pressroom mixed solutions and go to a so called “one-step” solution. This is simply a fountain solution additive that is comprised of the gum solution, the etch, and alcohol substitutes. It is mixed with water at press side or at a central area.
Two important key properties are fountain pH and conductivity. What is pH? Well in the Roman days they knew it as “potentia hydrogenii” or “potential for Hydrogen” thus the small “p” and capital “H.” Ph is a measurement of the degree of acidity or alkalinity of substances. Ph is important for maintaining high-quality, trouble free printing. The purpose of the acid in fountain solution ensures that the action of the gum is reinforced and not destroyed. An acid such as phosphoric or citric in a sufficiently dilute form will, in combination with the gum arabic, liberate the arabic acid molecules from the gum and permit them to combine with the metal oxides (aluminum) on the plate. This results in the desired hydrophilic (water loving) surface of the non-image areas. This breaks down quickly but is reinforced every time the plate has the fountain solution reapplied (every turn of the plate cylinder). To keep the pH stable, as contaminates such as Calcium Carbonate, attempt to change the solution pH, buffering agents are added. These keep the pH stable during the course of printing.
The pH scale runs from 0 – 14 with 7.0 being the midpoint (neutral). A solution with a pH of more than 7.0 would be alkaline (the higher the number, the higher the acidity. A solution with a pH number less than 7.0 would be acidic. A whole-number change on the pH scale represents a tenfold change in pH. For example a pH 5.0 indicates ten times the acidity of a pH of 6.0. To measure pH, a good electronic meter should be used to assure accurate pH readings. Litmus paper can be used but is usually much less accurate.
Conductivity is the ability, or power, to transmit or conduct an electrical charge. In water or any solution the degree of conductivity is determined by the number of ions present as a result of minerals or other compounds in the water. Basically, the higher the concentration of ions the higher the degree of conductivity. Water generally has a very low ion level and, as a result, registers very low in conductivity reading. Hydrochloric acid (HCL) on the other hand has a high ion level and is an excellent conductor of electricity and produces very high conductivity readings. Alcohol, by the way, does not conduct electrical charges and has a conductivity reading of 0. Glycerine produces the same. Thus as a printer adds alcohol or glycerine, the solution will be diluted and the conductivity reading lowered. What does all this mean? It means that conductivity is a measurements of contaminates entering the fountain solution. As contaminates enter, the conductivity will rise.
To measure conductivity an electronic “conductivity meter” is used. Many are combined with pH meters so the printer can measure pH and conductivity at the same time. To unit of measure for conductivity is expressed as the “ohm.” Since the conductivity is usually low, measurements are usually expressed as a “micro-ohm.” Contrary to believe there is no “magic” conductivity number. The printer, in general, measures his base water for pH and Conductivity and records it. At an ounce at a time, he/she begins adding the fountain concentrate and re-measuring pH and Conductivity and records (charts) the readings. When adding a buffered acid concentrate to the water (in preparation of fountain solution), the pH will drop to a certain level and then plateau at that level, regardless of how much buffered concentrate is added. On the other hand, as more buffered fountain concentrate is added the higher the conductivity readings. The printer will continue adding, an ounce at a time, buffered fountain etch up to the point where they usually run. A chart is made showing pH, conductivity and number of ounces per gallon. This chart can be used for reference. If the printer, for example, found that they needed 4.5 Oz. of buffered fountain etch to a gallon of water and this produced a pH of 4.3 and a conductivity level of 1800 – that would be their base.
The printer should measure pH and conductivity at least twice a shift and tack the readings. Measuring only once and a while will give no indications of problems. Tracking pH and conductivity, however, will begin to show problems. For example, if a printer starts to see a rise of conductivity from 1,800 to 2,000 not much contaminates are entering the fountain system. If on the other hand they see a rise in conductivity from 1,800 to 3,000 they can expect problems as a high amount of contaminates are entering the system. These contaminates can interfere with fountain solution materials and results in effective nonimage protection which results in scumming, toning, tinting, etc.
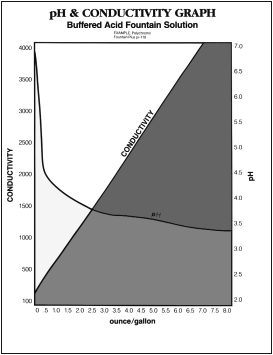
Water hardness is also very important as hard water contains Calcium and Manganese minerals. It is known that high calcium monorails will interact with the Calcium Carbonate in the paper resulting in “Milking” or “Whiting” of the blankets. Printers today should treat their water (soften. purify, etc.). Water is a raw material!!
Water hardness can be measured with the conductivity meter. For a rough guide to the conductivity of water of different hardness, refer to the below Water Hardness Table.
Water with hardness readings in excess of 29.2 grains/gal, or 500 mg/l or 500 PPm are unsuitable for Lithography.
In the past, and in some cases yet today, isopropyl alcohol was used in percentages as high as 20%. Alcohol was used to help the fountain solution “flow” across the dampening rollers. Isopropyl alcohol is also a very good wetting agent. This feature allowed the fountain solution to “wet” the plate very well. The government, however, has determined that IPA (isopropyl alcohol) is high in VOC뭩 (volatile organic compounds) and wants it eliminated from the pressroom. Alcohol substitutes have been developed to replace alcohol. Alcohol is not really needed in conventional dampening systems as they use the paper sleeves or fabric covers. Alcohol or alcohol substitutes work best in continuous dampening systems which have roll to roll contact.
Degree of Hardness | Grain/Gal | MG/L or PPM | Conductivity Micromhos/cm |
SOFT | 0 – 7.9 | 0 – 135 | 0 – 225 |
MEDIUM | 8.0 – 15.9 | 136 – 272 | 226 – 450 |
HARD | 16.0 – > | 273 – > | 451 – > |
Alcohol substitutes are all proprietary mixture of solvents. Even though alcohol substitutes are proprietary mixtures they do have a couple of common traits that should be considered:
- First, they are strong ink solvents.
- Second, they are very non-volatile.
Because of this combination of properties they tend to remain in the fountain solution and, at the same time, can extract some oil portions from the ink. Eventually this can contaminate the dampening system. For this reason it is very important that the dampening system be thoroughly cleaned on a regular basis.
A final characteristic of the fountain solution to be considered in keeping the ink formulator aware of the parameters on the press, is the pH. In normal printing, virtually all fountain solutions are maintained at an acid pH, that is a pH below 7. The most common method of controlling pH is with a pH meter or pen which is usually sufficient. However, to insure that the proper concentration of etch is being utilized, “conductivity” measurements give an unambiguous indication of etch concentration. The electrical conductivity or conductance of fountain solutions is quite sensitive to changes in concentration. Therefore, use of conductivity as a control of etch concentration is superior to pH.
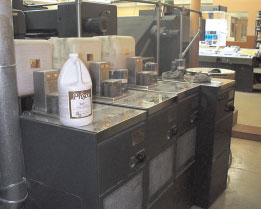
Typical fountain tanks feeding several printing stations. Usually, each printing station will have it뭩 own fountain tank.
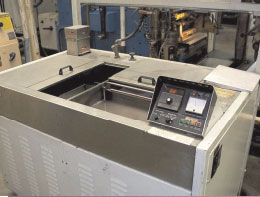
Typical fountain tank used on a heatset web. This type of unit will feed all printing stations. The unit displayed to the right generally holds a total of 50 gallons of fountain solution.