There are four key ingredients in an ink:
- Pigments
- Solvents
- Vehicles
- Additives
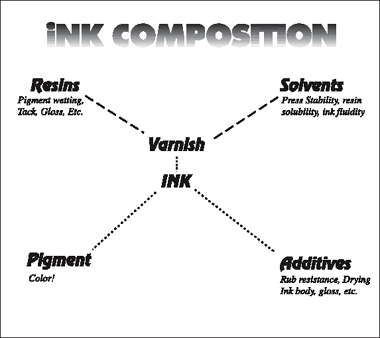
Pigments – These are dry particles that give color to ink. There are various types of pigments such as organic and inorganic. Organic pigments contain carbon and hydrogen and most are made from petroleum. Coal, wood, animal fats, and vegetable oils are also used in organic pigment manufacture. Generally there is a wider selection of colors in relationship to inorganic pigments. Colors tend to be richer, brighter, and more transparent. Inorganic pigments are chemical compounds, typically formed by precipitation. Pigment color is determined by theproportions of the chemicals used to produce a pigment. Cadmium yellow, for example, may contain the chemical cadmium sulfide in a compound with zinc sulfide. Ink made with inorganic pigments are less expensive to produce than those made with organic pigments. They give good opacity but lack some of the qualities of organic pigments inks, such as transparency.
Pigments are classed as opaque and transparent pigments. Opaque pigments are used when transferring an image to cover a substrate or when overprinting another color. Opaque whites are also used for mixing with other inks to lighten the color or hue. Many times a printer will print opaque white to help “hide” the infl uence of a dark color paper on the overprinting ink. For example, if the printer was printing a job on a dark brown paper, he may first print a mask of the images in opaque white then over print his colors. If he did not do this, the dark brown color of the paper would infl uence the color of the ink. Transparent pigments are used to allow the background material or ink to be seen. All process colors (black, cyan, magenta and yellow) are transparent. Process inks need to be transparent to allow the proper tapping mechanism to occur. For example, to create green we must print cyan and yellow. By printing cyan and then over printing yellow, the result in green. If the inks were opaque, when printing the yellow on top of the cyan, the opaque yellow would hide the cyan resulting in the final color being yellow!
Vehicles – Vehicles are made with resins (to promote pigments wetting, tack, gloss, etc.) and solvents (press stability, resin solubility, ink fl uidity, etc.). The vehicle portion of an ink is the liquid portion that holds and carries the pigment. It also provides workability and drying properties and binds the pigment to the substrate after the ink has dried. Each vehicle used in the manufacture of ink has a slightly different composition. Non-drying vehicles used in newspaper and comic book production are made from penetrating oils such as petroleum and rosin. Oils are classed as to how fast they “dry”. Linseed oil, for example is a faster drying oil than soy. Quicksetting inks used for sheetfed offset consist of resin, oil and solvent. During the drying process the solvent is absorbed by the substrate, leaving an ink film of resin and oil that dries by oxidation. Heatset inks are made from rosin ester varnishes or soaps and hydrocarbon resins dissolved in petroleum solvents. The solvents are driven off in the heatset oven, and the resins “set” by the action of the cold chill rollers.
Ink Additives – Listed below are some of the more common ink additives:
- Reducers: Varnishes, solvents, oils, or waxy or greasy compounds that reduce the tack or stickiness of ink. They also aid ink penetration and setting.
- Driers: Metallic salts added to inks to speed oxidation and drying of the oil vehicle. As noted earlier, these include cobalt and maganese driers.
- Binding Varnish: A viscous varnish used to toughen dried ink film. Can increase image sharpness, resist emulsification, eliminate chalking, and improve drying. Remember, over emulsification occurs in offset litho when excessive fountain solution mixes with the ink. The result of emulsification is an ink that actually appears to break down and becomes greasy looking.
- Waxes: Usually cooked into the vehicle during the manufacturing process or can be added to the ink later. Paraffin wax, beeswax, carnauba wax, microcrystalline, ozokerite, and polyethylene are commonly used. Wax helps prevent setoff and sheet sticking. Wax also “shortens” the ink or limits its ability to stretch or web.
- Antiskinning agents: Prevent ink on ink rollers from skinning and drying. If these agents are used excessively, the ink will not dry on the paper. These are also known as antioxidants. Printers will use them on the inking system if the press shut down for a period of time. You will see the press use a spray can on the ink system just after shutdown.
- Cornstarch: Can be used to add body to a thin ink. Also helps prevent set off.
Types Of Lithographic Inks
As you can imagine, there are many types of ink formulations to serve the offset or lithographic industry. The attached table show the various ink formulations for different presses and substrates. A variety of vehicles are required because of the differences between sheet and web feeding and because of the many substrates on which the printer must transfer images.
Some of the key offset inks include:
Rubber-Base Offset Ink – This ink is a heavy formulation that gives quick setting and drying on both coated and uncoated paper. It can remain on the press for long periods without skinning. Printers will leave these inks on the press overnight without the fear of skinning or drying. These inks are, by far, more popular with quick printers using small duplicators.
Nonporous Ink – An ink formulated with a nonporous vehicle. These inks are suited for plasticcoated or metallic type of papers. They dry by oxidation rather than by absorption. Ink additives are not recommended with this ink formulation. To prevent set-off, do not allow a large pile to accumulate in the stacker and use small amount of spray powder.
Quick-setting Inks – Quick-setting, low tack inks are formulated with the color and process printer in mind. Quick setting ink relys on rapid separation of thin mineral oil from the ink film followed by oxidation/polymerization of the drying oil. The quickset vehicle is composed of two phases which are of limited compatibility. One phase is a highly viscous solution of hard resin in drying oil, and the other phase is very low viscosity petroleum distillate. The resin/drying oil and distillate must be sufficiently compatible for the vehicle to remain as a stable, homogeneous fluid throughout ink distribution and transfer to the substrate on the press. Once deposited as a thin film on absorbent paper or board, a capillary-draw mechanism pulls the highly mobile distillate away from the rest of the ink. If the two phases are too compatible, the affinity of the resin/oil for the distillate will inhibit this penetration and slow drying occurs. If a limited compatibility exists the distillate will be separated from the ink and will be drawn into the interstices of the substrate coating or fiber network leaving the hard resin in drying oil (or alkyd) phase binding the pigment on the print surface. While not fully dry, the ink film reaches such a high viscosity that is loses mobility and ceases to transfer readily. At the stage the ink is said to be “set” and will not mark the reverse of the subsequent sheet in a stack. Setting may take from 2 mins to over 1/2 hour depending on the ink formulation, the printed film weight, the nature of the par or board substrate and ambient conditions.
After the ink is set, oxidation drying within the drying oil or alkyd, and possibly the resin, leads to polymerization and the formation of a three dimensional cross-linked network of chemical bonds. Depending upon many conditions (temperature, humidity, acidity, etc.) this chemical reaction is usually well advanced in 9 – 15 hours, although it may take a matter of day to reach total completion!Waterless Sheetfed Inks – These inks are used in the modified lithographic process where no fountain solution is used. The key to this process is a technique is a plate that consists of two layers, a photopolymer layer and a silicone layer. The ink chemical nature of the silicone resists the ink and keeps the nonimage areas of the plate clean. The key to waterless printing is ensuring that the ink film is more attracted to itself than it is to the silicone of the nonimage areas of the plate. To perform this task the inks are formulated with special resins and other additives to produce higher viscosities than are found in conventional lithographic inks. Because the ink’s viscosity is affected by temperature, waterless lithographic presses must carefully regulate the temperature of the ink and control the tendency of ink to lose viscosity from friction-generated heat in the ink train. Most waterless inks have a temperature “window” where the ink runs. Get outside that window and the ink may start scumming, toning, piling, etc. To regulate the ink’s temperature, the ink system for each unit is controlled by a control system, which is usually sitting along side the press. An infrared sensor on each printing units ink system tracks the inks temperature. If the ink roller system, for example black, gets to hot cold water is passed through the black ink vibrators; get to cold and hot water is passed through the rollers.
Sheetfed PressesSubstrates – Paper, Foil, Film, Thin Metal | Web PressesSubstrates – Mostly Paper |
Ink Vehicle Class Oxidative – Neutral or synthetic drying oils. | Ink Vehicle Class Oxidative – Drying oil varnish |
Penetrating – Soluble resins, hydrocarbon oils & solvents, drying and semidrying oils and varnishes. | Penetrating – Hydrocarbons, oils & solvents, soluble resins, drying oil varnishes, and plasticizers. |
Quickset – Hard soluble resin, hydrocarbon oils and solvents, minimal drying oils and plasticizers. | UV Curing – Highly reactive, cross-linking proprietary systems that dry by UV radiation. |
UV Curing – Highly reactive, cross-linking proprietary systems that dry by UV (ultra violet) radiation. | Thermal Curing – Dry by application of heat and use of special cross linking catalysts. |
Gloss – Drying oils, very hard resins, minimal hydrocarbon solvents. |
Heatset Inks – These inks are used in heatset web offset presses and require the use of an oven and a chill roll section. The “oven” drives off the fresh ink liquid solvents and the “chill roll section” (series of cold rolls), solidifies the remaining pigment-in-resin component. The typical heatset ink is usually made up of hydrocarbon solvents, hard soluble resins, drying oil varnishes and plasticizers along with pigments. As the inks require heat to drive off the solvents, no driers are added like in sheetfed inks thus they can be left in the ink sump for extended periods of time if needed.
Metallic Inks – use metallic powders, such as aluminum and copper alloys, mixed with the proper varnish base to give a pleasing metallic luster. This is because the powders are actually fl akes which deposit in refl ective layers. The bronze powder and vehicle for preparing gold inks are mixed just before using. The varnish dries rapidly and has sufficient binding qualities to hold the powder to the paper surface. Coated papers give the best results. On rough paper surfaces, a base ink is usually printed first, allowed to dry and overprinted with gold. Both aluminum and gold inks can be printed by letterpress, offset or gravure. When printed by offset, alkaline or neutral fountain solutions should be used to prevent tarnishing of the bronze powder.
Magnetic Inks – were developed to increase the speed and efficiency of handling bank checks. These ink are made with pigments which can be magnetized after printing, and the printed characters are later “recognized” by electronic reading equipment.
Fluorescent Inks – were formerly limited to screen printing. New finer grind pigments and greater pigments strength now permit colors to be printed in one pass. The semi-transparency of the inks permits overprinting to achieve color mixture. Fluorescent ink must be printed on a white surface and provide maximum brilliance when contrasting with dark surrounding hues. Fluorescent pink is used as a fifth color in 4-color process printing to enhance skin tones and extend the range of magenta hues in the images.
Dye Sublimation Inks – These inks are used widely in textile printing. The “dye-sub” process works like this: When the correct heat and pressure is applied, the ink passes (or sublimates) form a solid to a gas, never passing through liquid form. Once in gaseous form, it dyes or stains whatever is next to it. On a molecular level, it becomes part of the substrate and will not peel away or fade faster than the fabric itself. The ink doesn’t sit on top of the material so it doesn’t wear off and usually fades or breaks down in the same rate as the fabric does. These special inks are usually printed using the lithographic process onto paper. The printed paper is then pressed against the fabric and heat applied. Today ink jet printers can also do this. Home users can, today, also do “fabric printing” by using “Tee-Shirt Transfer” material, such as Hammermill’s “Invent itTM” ink jet transfer product. Once ink-jet, heat is applied and the dye transferred on to the fabric. While good, the lithographic dye-sub process is far superior.
There is a drawback with dye sub in that the substrates must contain a portion of synthetics, like polyester and nylon. This is because the textile dyes must sublimate at 410 degrees Fahrenheit to transfer the print from the paper to the fabric.
Radiation Curing Inks – have been developed to eliminate spray powder in sheetfed printing and air pollution from solvent is conventional web heat-set inks. There are two types of these inks: Ultraviolet (UV) and electron beam (EB) curing.
UV curing inks consist of liquid prepolymers and initiators which on exposure to large doses of UV radiation release free radicals that polymerize the vehicle to a dry, solid, tough thermosetting resin. These inks are, however, more expensive than standard inks and are used mainly for luxury packaging, metal decorating, screen printing, and coating.
Electron beam (EB) – curing inks make a good alternative to UV inks since no expensive initiators are needed and some lower cost, less reactive materials can be used. The major disadvantage of EB is the high capital cost of equipping a press to use it. EB uses less energy than UV, which in turn uses about half the energy of gas drying.
Varnish and Lacquer – materials are used as coatings over printing to protect the printing and increase the gloss. Ink makers should know when printing will be lacquered so that ink can be formulated to be lacquers resistant. Otherwise, the ink are apt to bleed through the varnish or lacquers. Inks to be varnished or lacquered would not contain waxes which can prevent wetting, or adhesion of the varnish or lacquer to the ink. Also minimal spray powder should be used on sheet to be varnished or lacquered since the powder can affect even transfer of the varnish or lacquer.
Lacquers are applied off-line on special coating machines. A variety of press applied varnishes and devices for on-press application are available. Most press varnishing is done from a blank or imaged plate inline with the printing on the press, and drying is by oxidation without heat. Gloss and their special characteristics are limited as the varnishes must be compatible with the wet inks.
Overcoatings – are used to replace off-line varnishing and eliminate the need for anti-set-off starch sprays, which are yhe scourge in the pressroom. Acrylic type emulsions with water and alcohol and varying degrees of gloss are coated over the wet inks on the image inline with the printing. The resin coats the ink, while the water or alcohol disperse in the paper. The coatings dry rapidly preventing the wet inks from scuffing or marking while they dry normally. UV curable clear coatings are also used as overcoatings on the printing inks. The ink may need reformulation to be compatible with the UV overcoatings.
A disadvantage of press overcoating has been the need for an additional unit on the press to apply the coating. The use of overcoatings has become so popular, however, that most new sheetfed presses can be built with special coating units or towers for controlled inline application of the coatings.
Water-Washable Inks – have been developed by Deluxe Checks are are “water washable” so no solvents are needed. The inks when used on press are stable and not soluble with the fountain solution. pH is the key for making the inks water washable. The ink is acidic and resists water. Once the swing in pH is made, to alkaline, the ink become soluble in water. The cleaning material, mostly water, contains conversion material to make the ink water washable. Advantages of these inks include:
- No solvent vapors
- No fl ammability
- Potential for increased EPA compliance
- Reduced Hazardous waste
- Potential to sewer wash ink/waste solution
- Improved market position with environmental conscious customers
As of this writing, these inks are only suitable for non-heatset web presses, however, beta testing is being conducted on sheetfed and heatset web.
The following is are common additives used in a sheetfed pressroom to alter sheetfed offset ink:
- Smooth Lith – A liquid that controls lay and set-off.
- Reducing Compounds – Cuts the tack of ink without changing its body (viscosity).
- #00, #0 Litho Varnish – A thin bodied compound that rapidly reduces the ink’s body.
- #1 Litho Varnish: reduces tack and body – used as a lay compound and prevents picking.
- #2, #3, #4 and #5 Litho varnishes – Increase the ink fl ow without changing the ink’s body.
- Overprint varnish – A gloss, satin or dull finish used to print over already printed ink.
- Dryers – See above – To enhance the inks drying ability.
- Luster binding base – Builds up viscosity, gives ink a luster finish and makes ink more water repellent.
- Aqua varnish – Builds up body and tack of an ink.
- Body gum – A heavy varnish that increases the ink’s body, tack, and water repellency.
- Gloss varnish and wax compound – Increase the ink’s resistance to scratching and scuffing. Gloss varnish gives ink a bright finish and helps prevent chalking on coated papers.
There are other additives used by printers, but the above are the normal additives used.