The conventional offset process contains a plate cylinder, a blanket cylinder and a impression cylinder. A ink and dampening (fountain) system to supply ink and fountain solution is also included.
The press prints only one side of the substrate at a time. If you wish to print the other side of the sheet, you must turn the sheet over and re-print it. The impression cylinder is adjustable to accommodate the various calipers of substrates or to place more pressure between the blanket and impression cylinder. This helps in printing embossed type papers.
The plate cylinder receives the ink and fountain then transfers it to the blanket cylinder which in turn transfers the image to the substrate thus “offset”.
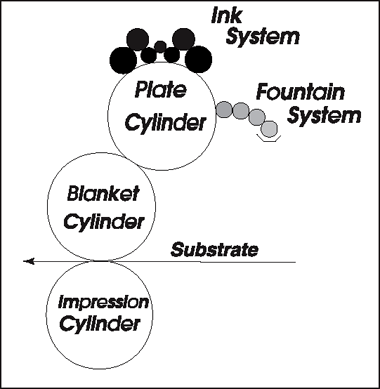
The perfector offset press is similar to the conventional press except it has a mirror image of itself underneath. The impression cylinder of the top and bottom are the opposite blanket cylinders. Perfector type presses are used in high-speed web printing. Small webs, such as Didde or Stevens, still use the conventional methods (above). High speed webs just as the Harris M1000B, M110, etc. use this method.
The perfector system prints both sides of the substrate at the same time. The printing nip is not manually adjustable but opens under the pressure of the substrate.
Some sheetfed presses may be known as “perfectors” but their makeup is conventional. The press can at one printing station can turn the sheet over so that printing on the back side. If a Sheetfed press is a 4-color press, perfecting between the 2nd and 3rd cylinders, two colors can be placed on each side.
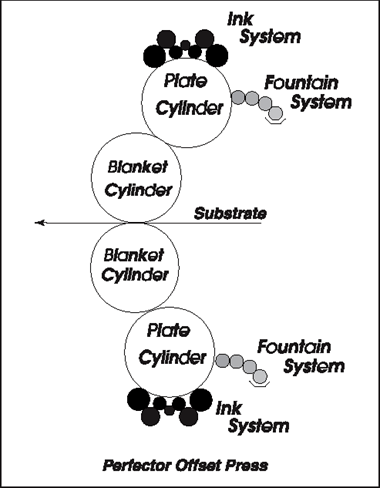