“Flexo” – A branch of letter press, flexo is a relief process but differs in the composition of the image carrier, ink and the method of ink application.
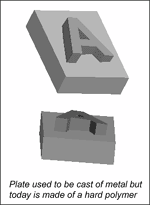
The image carrier may be a molded rubber plate, a photochemically produced photopolymer plastic plate or an image etched into a rubber roller.
Low viscosity inks (both water and solvent) are used in flexo printing. A simple ink metering system is used. An “anilox” roll is a knurled roll with wells carrying a fixed volume of ink to the printing plate. The number of cells per linear inch determines ink carrying capacity. A coarse anilox may have 120 cells per square inch while an anilox roll used for fine halftone reproduction might have 500 cells per inch. Anilox rolls may be chrome plated, ceramic or plasma arc sprayed ceramic for long wear.
In the early 1950’s this type of printing was known as Aniline printing since the “inks” were made with aniline dyes. It was found that many of these dyes were
carcinogenic. The industry quickly developed pigment based inks but the name stuck. As a majority of printing was done on packaging the buying public did not forget the dye problem and was very hesitant to purchase packages printed with this process. The industry quickly changed the name to “flexography” as the plate was flexible.
Flexo, today, is primarily used for packaging, labels, wall covering, wrapping and envelope printing. Single color book printing is done on a hybrid flexo press that combines flexo with letterpress also is known as the Cameron Book press.