All presses are composed of four basic units: feeder, registration, printing, and delivery. It is important that you understand the process a sheet of paper goes through in its trip from the infeed pile through the registration system to the printing unit and finally to the delivery pile.
The Feed Unit: The simplest and most common sheetfeeding system is Pilefeeding. With this system a pile of paper is placed on a feeder table while the press is off. As the press begins to run, each sheet is removed from the pile and the press moves the table up so that the top of the pile remains at a constant height.
To feed the paper, most sheetfed presses today use what is known as stream feeding. Stream feeders pickup and move the paper in a steady stream with each sheet over lapping the other. An air blast is used to separate the top sheet from the rest of the pile. This blast can be adjusted for papers of different weights and for different atmospheric conditions.
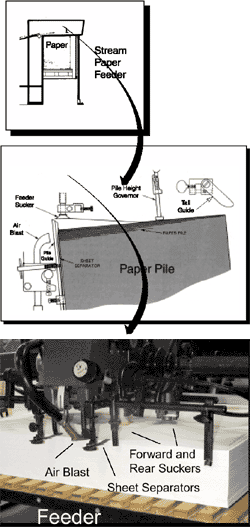
Once the top sheet has been slightly separated from the pile, a set of sucker feet pick-up and begin to move the sheet into the registration board where the registration unit takes over. The sucker feet are small vacuum tubes with rubber skirts. The amount of vacuum in the sucker feet can be adjusted for the type and weight of paper being used.
In actual operation, the sucker feet grab the top sheet from the pile and move it forward a short distance where it is picked up by pull-in wheels that put it squarely on a conveyer belt system on the registration board. The press automatically controls the precise moment when the sucker feet grab the top sheet, their movement toward the registration board, and the time when the vacuum is cut off and the sheet enters the registration unit.
As the press removes paper from the infeed table, the height of the paper pile decreases. The press automatically moves the infeed table up which then moves the pile closer to the sucker feet. There are also usually additional tools to assist in the feeding of paper. Devices such as sheet separators and blow tubes are usually attached. Sheet separators are small thin metal strips which assist in the separating of the top sheet from the others. Blow tubes are side mounted near the edge of the pile. Small blasts of air (from the blow tubes) also assist in separating the top sheet from the others. Registration Systems: Registration is the process of controlling and directing the sheet as it enters the printing unit. The main goal of registration is to ensure absolute consistency of image position on every sheet printed. The term fit refers to the image position on the press sheet. Registration refers to the consistency of the position of the printed image during printing.
After leaving the infeed pile, the press sheet is moved along the registration board. The registration board (also known as the feed table) consists of a conveyer belt system and some type of registration system. The conveyer belts carry the paper to the registration unit, where it is momentarily stopped and squared to the plate cylinder along the top edge by a headstop. At the same time, it is either pushed or pulled slightly sideways and placed in the proper printing position. The device to pull or push the sheet into position is known as a side guide. Adjustments can be made on the side guide to affect or change the proper registration.
It is at this phase in the printing cycle that sheet squareness and stability is important. If the sheet is not square, for example, the sheet will print fine on the first pass but if printing on the backside the sheet will not line up front-to-back. This will mean the fold or cut marks and front to back page alignment will be out. The result, of course, will be a rejection by the printer. The printer can in some cases 밷ack-trim?the sheets to 뱒quare?them up. Sheet porosity (Gurley) is also important. To low a porosity (Gurley <5) may cause problems as the feed suckers may pick up more than one sheet due to the openness of the sheet.
Many printers like grain long (fiber aligned in the long dimension of the sheet) or grain short (fiber aligned in the short dimension of the sheet). There are positives and negatives to both. Grain long will be less prone to 밼anning?problems (see glossary) or less prone to registration problems. This would be important if printing a multicolored job. On the other hand since the grain is in the long or cross direction, say a 19?x 25?sheet, the sheet will have a tendency to 밹url?or 뱑oll?over and jam in the feeder or transfer unit. The sheets will also have a tendency to 뱑oll?over in the delivery stack. Paper that is printed grain short will not have the tendency to curl or roll over since the grain is going in the machine (press) direction. The sheet will, however, have the tendency to fan out or in as the fiber is aligned in the machine direction and can be 뱎ushed?or out or in during the printing process (due to nip pressure). Printers will also use grain long or short depending on the type of work they are doing. If printing a book, for example, they will purchase the paper grain direction based on fold in the book. The printer will want the grain to be parallel to the binding edge. Pages bound with the grain perpendicular to the binding edge to not lie flat or turn easily. The printer will take all this into account when planning paper for press.