“Cold-set” presses are generally in the 17-inch wide range. This of course varies as large newspaper presses today are also mostly “cold-set.” These “baby webs” have been used mainly by the business forms printer to print forms that in most cases contained very little printing. This is why many forms printers were called “converters” as they tend to “convert” the forms. Today the fastest dying print market is the forms market. This is due to the laser since today many business forms are generated on a laser. Take, for example, a hotel receipt. In years past the hotel generated a two or three part carbonless (no carbon required) form. Today many hotels generate one or two laser copies instead. Restaurants are doing the same. The customer used to receive a two part form, if paying by credit card, which was known in the forms industry as a “guest check.” Today the consumer receives a laser receipt or a non-printed carbonless or thermal form.
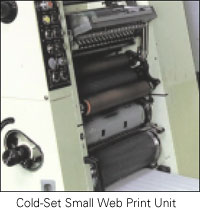
The digital market (Xeikon, Indigo, etc.) is also impacting the forms market today as these presses can print 4-color as well as variable information. The Internet is also impacting the forms market with on-line forms and on-line consumer buying. So what are the forms printers doing about all this you ask? Well, they are now moving into the “Direct Mail Market” as well as printing commercial work. At one time the print markets were segregated by commercial, forms, etc. The lines are becoming blurred today as forms printers print commercial and commercial printers add low end forms. The big forms manufacturers such as Standard Register or Moore are moving in other directions thus subcontracting low volume forms to smaller forms printers.
Cold set press today instead of printing the traditional business form is now printing higher volume direct mail such as advertisements, coupons, etc. One might think direct mail is dead due to the rise of the Internet, however, the market is on an increase. Even Internet on-line companies such as Amazon.com use the printed direct mail market to advertise! The two medias can work together! The coldset press manufactures today are even gearing their small webs to compete against sheetfed. Their motto; “Why print 12,000 impressions per hour when you can print 40,000?” It is because of this shift that the smaller press are being equipped with press consoles, IR or UV driers, better registration systems, etc.
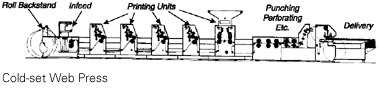
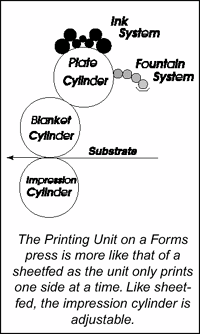
So how does the cold-set press differ from the larger heatset version? Cold-set web implies that the ink is not dried by heat but by absorption and/or oxidation. Cold-set web presses are smaller presses and generally used for business forms printing. Press sizes from 11″ to 25″ is common. While many of the functions of the cold-set press are similar to that of the Heatset web, they usually are not as complicated. As they do not need heat, no oven is needed. Small forms press also do not usually contain a folder section. They will, however, include a sheeter and can run roll-to-sheet or roll-to-roll (for future processing). The following is a breakdown of the smaller cold-set press:
- Unwind stand – The unwind sections are smaller and in most cases do not have automatic splicing sections. Generally, a roll is run until its completion. The press is stopped and the spent roll taken off. A new roll is then placed on the unwind stand an manually spliced into the remaining web and the press restarted.
- Web Tensioner – Very similar to that of the Heatset web press except that the unit is usually smaller. The same function applies – to control the in-feeding of the web.
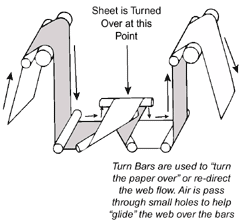
- Turn Bars – Many small forms presses utilize 뱓urn bars?which turn the web over. Many presses are confi gured with 5 printing units. The printer will print one color on the back of the web, then turn the web over and print the remaining 4 colors on the front. If a printer was printing a newsletter (both sides) he would print, depending upon his confi guration, one or two colors on the back, turn the sheet over and then print the other colors on the top.Turn bars are metal bars laid horizontally at a 45 degree angle from the web direction of the press. There are generally two bars. Most turn bars have small air holes so the a cushion of air assists in “gliding” the web over the bars.
- Printing Units – While the printing units are similar to that of the Heatset press, most small cold-set presses utilize a blanket to impression system printing only one side. Like sheetfed presses, the impression cylinder can be adjusted to provide maximum printing performance. All other aspects of the printing unit, are similar to that of the larger Heatset press. Many direct mail presses will use blanket-to-blanket systems and be slightly wider.
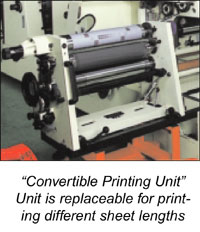
- Perforating, cutting, punching, etc. – Most forms type presses have units following printing that will imprint numbers, MICR codes, punch holes, perforate the web, etc.. Imprinting units are small, usually rubber plates used for printing fixed information on a form. Frequently, each of the offset units prints the same information on the paper web and the imprinter designates the receiver of each part of the form, such as Receiving, Purchasing, Manufacturing and Sales.
Next the web may be printed by a numbering unit, with regular Arabic numbers if the forms are to be consecutively numbered, or with special MICR or OCR numbers. There are two types of numbering heads; fl at heads for numbering across the web, parallel to the horizontal perforations on continuous forms or at right angles to the stub for unit sets; and barrel, or convex, heads, used for numbering parallel to the web travel.
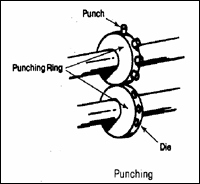
The printed web can then be punched. Punched holes are used in both continuous and unit sets to control registration from part to part on the forms collator. Marginal punches for continuous forms have been standardized by the industry so that forms can be run on any type of equipment regardless of the equipment maker.
In addition to marginal punching, forms may also be punched for fi le, loose-leaf, or register machine holes. These differ in their punching requirements, both in the hole size and spacing, so several different punching heads are needed. Marginal punching is a precision operation; the holes must be in perfect alignment along both edges, with a tolerance of only plus or minus 1/4 of 1%. Punch units must match the plate cylinder size in order to maintain register with holes exactly 1/2″ apart. This is known as “throw length.”
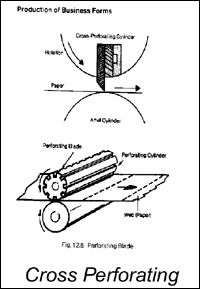
Perforating the web follows punching. There are both vertical and horizontal perforators. Vertical perforations are put in with wheels mounted on shafts. Their purpose is to provide easy removal of the line hole punching on continuous forms or on the stub punches of unit sets. The tear strength of this perforation is determined by the number of slots per inch. The greater the number of slots on the wheel, the more ties will be left on the form and the stronger the perforation will be.
Horizontal, or cross, perforations are made by perforating blades mounted in slots on a cylinder. This cylinder has the same circumference as the plate cylinder and has several slots in order to accommodate a choice of form lengths. This type of perforating is very demanding and depends on the weight and strength of the paper, stresses encountered on the press and collator, and the method used to break the forms apart. Like vertical perforating, the tear strength of the perforation is determined by the number of cuts per inch and the depth of the cuts. The fewer cuts per inch, the stronger the perforation and the deeper the cuts.
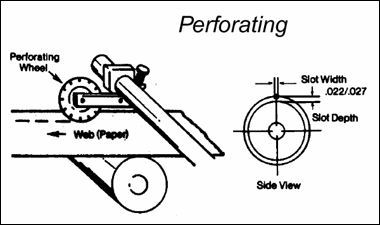
- Scratch-Off ink, used mostly in direct mail printing, is usually applied just following the printing and prior to perforating, punching, etc. Scratch-off inks are usually gold or silver. They are applied to hide a piece of printed information. The consumer “scratches off” the ink with a coin or finger nail to reveal the printed information. Scratch-offs are usually used for lottery tickets, sweepstakes, etc.
Many direct mail and forms presses use interchangeable printing cylinders to accommodate different printed sheets lengths (cutoff). Many direct mail presses, which are very similar to a forms press, with perforating, punching, etc., will be heat-set for greater speed. This presses tend to be in the 17-28″ wide range.
Typical Business Form presses which ran print roll-to-toll or roll-to-sheet
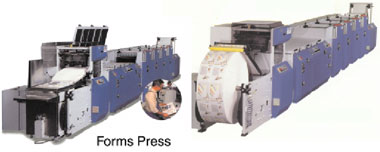