Heatset implies heat. To set and dry the ink, heat is applied via an drying oven which evapo-rates the solvents in the ink. After the printed web passes through the oven, the web passes a series of chill rolls that cool the web and set the ink. Most heatset commercial web presses are blanket-to-blanket, thus printing both sides of the paper at the same time. A blanket-to-blanket web press contains a printing unit on top and a mirror unit on the bottom. The blanket of the bottom unit is the impression for the top just as the top blanket cylinder is the impression for the lower unit. Unlike a blanket to impression cylinder, adjustments to the impression with the blanket-to-blanket press are completed through blanket packing (see the Offset Theory sec-tion).
The major components of the Heatset web include the following:
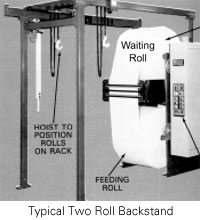
- Roll Stand – the roll stand holds one or two webs of paper and meters it into the press. Control of the web as it unwinds from the roll stand and enters the printing unit is established by a dancer roll which operates in conjunction with a brake on the roll stand. The infeeding web wraps around the dancer roller which actually rides on the moving web, pressing its weight against the moving paper. The dancer is free to move up and down; this movement controls a brake on the roll stand. If the web feeds to rapidly, the paper under the dancer roller becomes slack and the dancer roller drops, which automatically applies a brake to the roll stand, slowing the paper feed. If the web feeds to slowly, just the oppo-site occurs. The paper under the dancer becomes taut, lifting the dancer, which releases the brake on the roll stand, allowing the web to feed more rapidly.
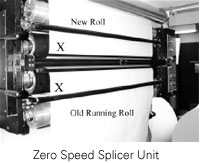
- Splicer – In addition to the dancer roller, it is common for a roll stand to include a splicer also referred to as a “paster” As implied, the splicer automatically positions a new web or infeed, and splices the lead end of this new web to the tail end of the web being printed. There are two types of splicers: Flying splicers and zero speed splicers (see next page). Both splicer units operate automatically, and both use adhesives (tape) to connect the two webs. The difference between them is that a flying splicer connects the two webs while each is rotating at press speed. It does so by pressing both the adhesive lead edge of the new web and the tail edge of the printing web against a splicing arm which then connects the two together. The zero speed splicer uses a festoon, consisting of several rollers. The festoon holds enough paper to feed the press during the splice. Thus the splice can be made while the printing web is moving and the new web stationary. Presses with widths between 23″ and 38″ use the zero speed splices where as presses over the width of 38″ generally use a flying splice. Many times it is advisable to apply “grease” at the edges of the web (Marked with an X in the photo) to help the web “slide” through the printing nips and not break apart.
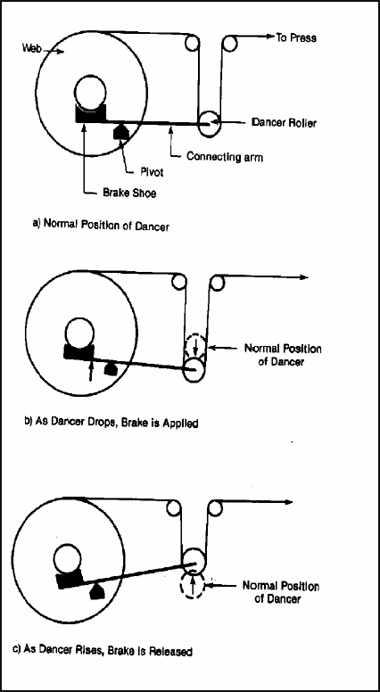
- Web tensioner – While the roll stand and dancer roller work together to meter the web as it enters the printing units, they cannot completely control web tension. Several factors, such as the tension with which the web was wound at the mill, the type of the paper or material to be printed, blanket packing, and the confi guration of the press itself affects web tension during printing. The dancer and break mechanism alone cannot adequately compensate for all of these fac-tors to maintain proper web tension. Improper tension can lead to improper image registration or even break the sheet causing a press shut-down.Most high-speed web presses employ a tensioner to maintain consistent web tension. The unit consists of a series of rollers over which the infeeding web passes. As the web passes over the tensioner rollers, it “recovers” from the tension with which it was wound at the mill, and it is regulated to the proper, even tension for the press run. Today, many tensioners consist of a series of variable speed rollers, followed by a second dancer roller. This ensures proper web tension with a minimum variation.
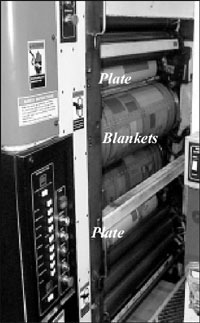
- Printing Units – Printing units are similar to that of any other offset printing press; inking unit, dampening unit, plate cylinder and blanket cylinder. Most high speed presses use the blanket-to-blanket arrangements so that printing of both sides of the web are possible. Some high speed presses (1200 to 2000 ft/min) use a plate/blanket arrangement known as a “two-to-one.” The blanket cylinder is twice the diameter of the plate cylinder. One of the draw-backs at higher speeds with web presses is what is known as “cylinder gap bounce.” The plate and blanket are rectangular and when attached to the cylinder, leave a “gap” along the width of the cylinder. At high speeds, this gap between the plate and blanket create a frequency bounce which, in turn, causes a harmonic vibration. With a two-to-one system, the large diameter of the blanket cylinder helps reduce this bounce. The newer high speed presses of today are using a “one-to-one” plate/blanket system and use a “tube” blanket to cover the blanket cylinder. With the blanket tube and no gap, speed increases are possible. See Press Console for more detailed info on Inking and Dampening.
- Oven Dryer and Chill Rolls – The oven drier and chill rolls work together to ensure that the ink on the printed sheet is dry and set to prevent ink set-off. The type of ink used in this type of press will not dry by air and absorption. To dry the ink, the web is passed, after the last printing unit, through a dryer, which brings the moving web up to a temperature of about 300 to 350 F degrees in a few seconds. This temperature is high enough to evaporate most of the ink solvent. It also softens the ink resins that will bind the ink pigments together. Following the drying ovens, the web passes into the chill rroll section. Chill rolls are a series of rolls containing water-cooled water. During chilling, web temperature is reduced to about 90 F degrees which is cool enough to set the binder and pig-ment, producing a dry print. Contrary to belief, the chill rolls do not put moisture back into the sheet.
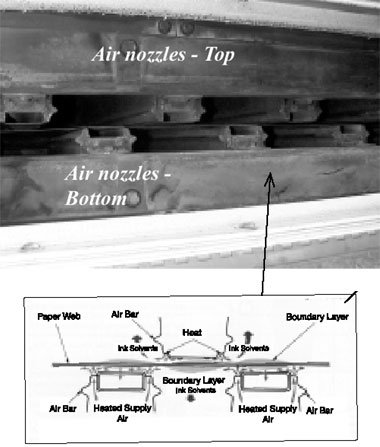
- Inside Oven – Air nozzles top and bottom supply hot air. Web “floats” in between.
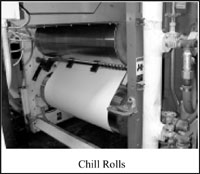
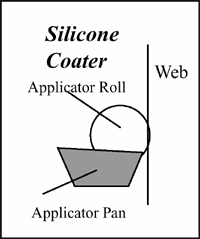
- Silicone Coater – Most high speed web presses contain one or two silicone roll coaters (much like a dampener). The unit(s) follow the chill rolls and can apply a water/silicone solution to one or both sides of the web. The application of a thin film of water/silicone is used mostly to reduce “marking” in folder units with coated papers. Coated papers, due to the latex coating, can acquire “marks” when passing through the folder unit. Uncoated papers benefit during the dry winter months if the printer adds a fabric softener to the water which, in turn, reduces web static.
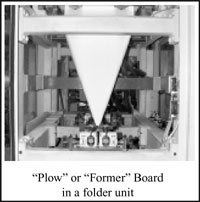
- Folding and Cutting – Most high speed web presses are equipped with one or more folders which fold the printed web into signatures (group of pages) as the web leaves the press. The type of folder depends on the type of work being printed on the press. There are three basic types of folders: former folders, jaw folders, and chopper, or quater folders. Often, all three folding devices are incorporated into a combination folder. A former folder folds the web by passing it over a triangualr-shaped former board. This action makes a “with the grain” fold by folding the web along it length. Additional folds after the former fold are made with jaw and chopper folders. A jaw folder folds the web across its width (cross grain) by allowing it to travel around a cylinder equipped with a tucker blade that forces the paper into a jaw (opening) on an opposing cylinder. After passing through the folding jaw, the web is automatically cut into individual signatures and, if necessary, passes to a chopper folder. In the chopper folder each signature is forced between two rotating fold rollers that make the final fold, against with the grain.Many web presses are equipped with a sheeter to allow the printer to cut the web into sheets for future post-press operations. The sheeter is a standard sheeter much like that of any rewinder. Many printed jobs do not need to be folded into signatures. For example, if the printer was printing very small pages, instead of 8.5″ X 11″, he would go into a sheeter and cut the small sheets off-line.
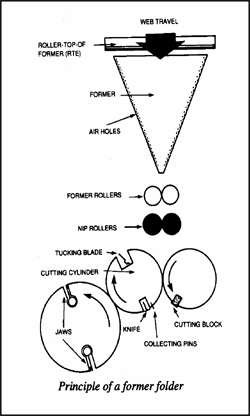
- Press Console – Most modern high speed commercial web presses have a press console. The press console provides electronic control for register, image control, ink and dampening easily. The press operator monitors the console and, if neceseasily. The press operator monitors the console and, if necessary, makes press adjustment by adjusting switches on the console, which cause the appropriate adjustments to be made on the press. Today, computer controlled consoles are the norm for process control and providing a consistent printed product.The color control console is where the printer will add or subtract color across the entire sheet or in localized areas. On the console are keys which correspond to “zones” in the inking system. Electronically the operator can select the color unit they want to change at the console. This will correspond at the selected print unit. If the printer wants more ink across the whole sheet, the ductor roll will contact the “feed” or “ball” roller longer. If the printer wants to only add color to a localized area, small plates at the ink fountain will open allowing more ink to pass at that spot only. This gives the printer great flexibility!
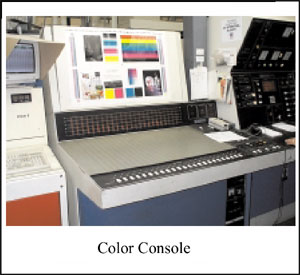
- To print; heatset web printers, unlike small web printers, will 뱎ump?ink from either large 뱓ote?bins or out of 55 gallon (400 lb) drums. Pumping serves several purposes among them being able to measure how much ink is being used for a job or what is known as “ink milage.” At the start of a job the press operator can set the pump recorder at “0” and at the end of the job read how many pounds of ink was used for black, cyan, magenta, yellow or any other special colors being printed.
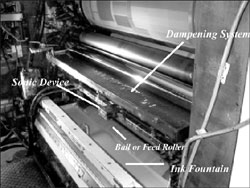
Ink/Dampening Unit
While this photo shows a lower inking/dampening unit, the top would be a mirror image.
As the ink is being pumped into the ink fountain the printer will, in most cases, use a sonic device to control the fl ow of ink. During printing ink level decreases, the sonic device senses it and calls for more ink. The level comes up and the sonic device shuts off the fl ow of ink. The press operator can set the low and high points of the device. This units will be sitting in the middle of the ink fountain just above the ink sump.
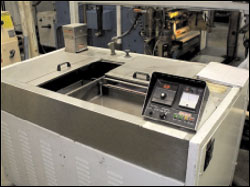
Fountain Tank
Tank holds 55 gallons of pre-mixed fountain solution. Meter in lower right corner measured conductivity and temperature. Settings on temperature are made at this point. Many systems can also measure pH.
- In dampening the large web printer will usually pre-mix their fountain solution in either very large pre-mix systems. Unlike sheet-fed where several small fountain chill units are used most large web pump fountain solution from one large fountain tank Many hold somewhere around 55 or more gallons of fountain solution. Like with the inking units a leveling device controls the amount in the tank. As the fountain level depletes more pre-mixed solution is added from the pre-mix tank. Fountain solution is pumped to all four units and recirculated back to the fountain tank for filtering (which helps clean out contamination from paper and ink). This is a constant recirculation process.
- It is typical for heatset web printers to use a lower tack ink on the fi rst unit followed by a higher tack then the succeeding units again lower. For example, black at a tack of 11, cyan 14, magenta 13 and yellow 12. This helps eliminate any “picking” tack issues and black is not a heavily “trapped” color. Printers will also alter ink for the type of paper they run. For example, higher tacks for coated, lower tacks for uncoated and very low tacks for supercalendered light weight publication grades. It is not uncommon, however, for a printer who prints mostly coated to run a standard ink for both coated and uncoated since they don’t want to take the time to change.
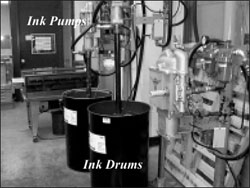
Ink Supply System
Each color is fed from a drum or tote system to the individual ink fountains. It is at this point the amount of ink being consumed can be measured.